Compound Formulation
RUBBER COMPOUNDING
It is a homogeneous mixture of ingredients used in a particular product manufacture such that the properties of most of the ingredients are unchanged in the final product whereby providing a defined set of mechanical properties.
Compounding:
It is the science of selecting and combining elastomers and additives to obtain an intimate mixture that will develop the necessary physical and chemical properties for a finished product.
Rubber compounding is a term covering a wide scope including the art and procedures that are necessary to produce useful products from natural or synthetic elastomers. A competent rubber compounder must be able to use the proper elastomers and additives available to meet the conditions required for the finished product. This requires a thorough understandind of the following:
Properties of the elastomers available.
Vulcanizating systems to give the potential properties needed.
Modifying materials which give the required physical properties and aging resistance.
Compounds must be able to process properly depending on the processing equipment.
Commercial compound design.
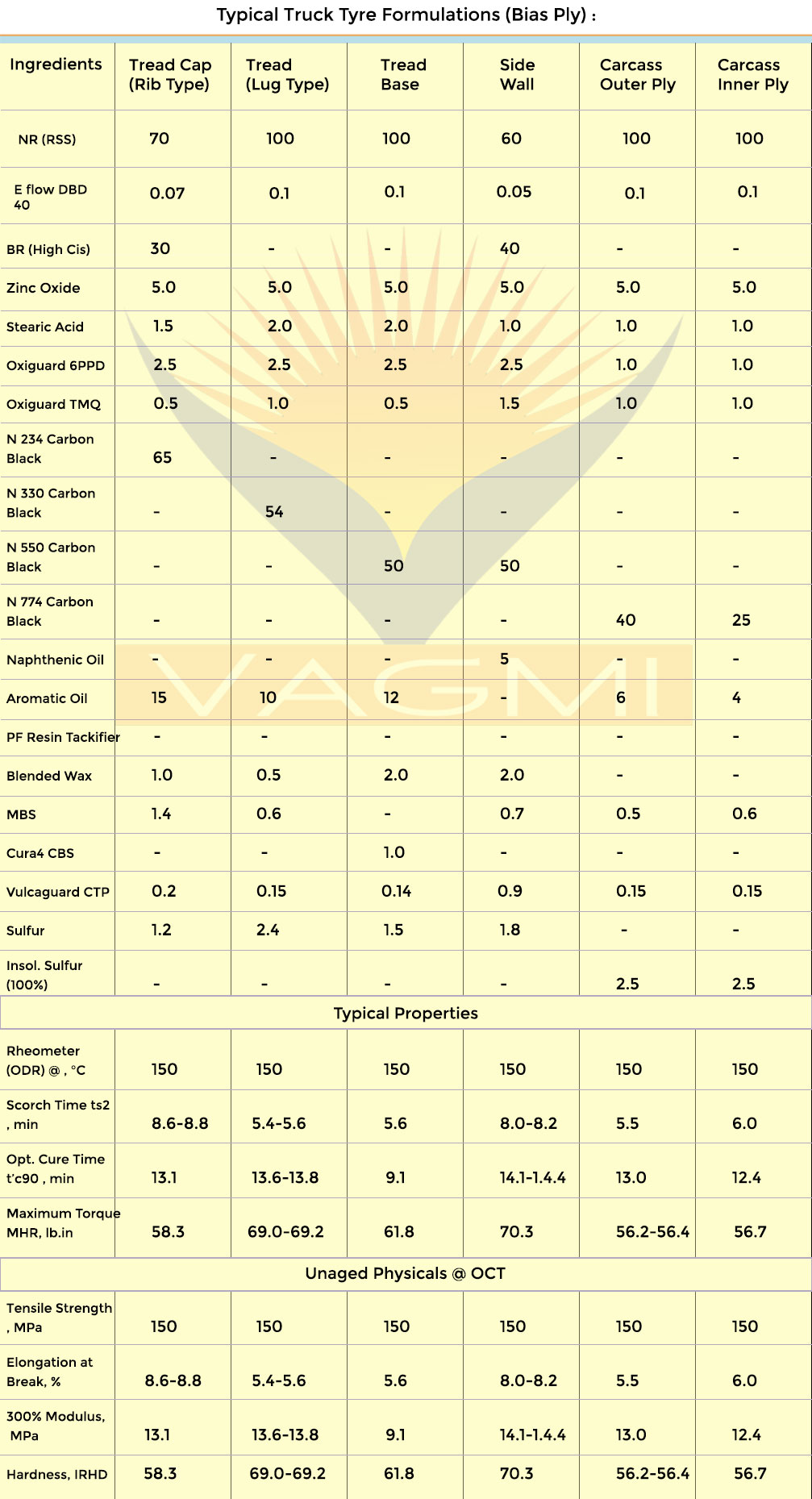
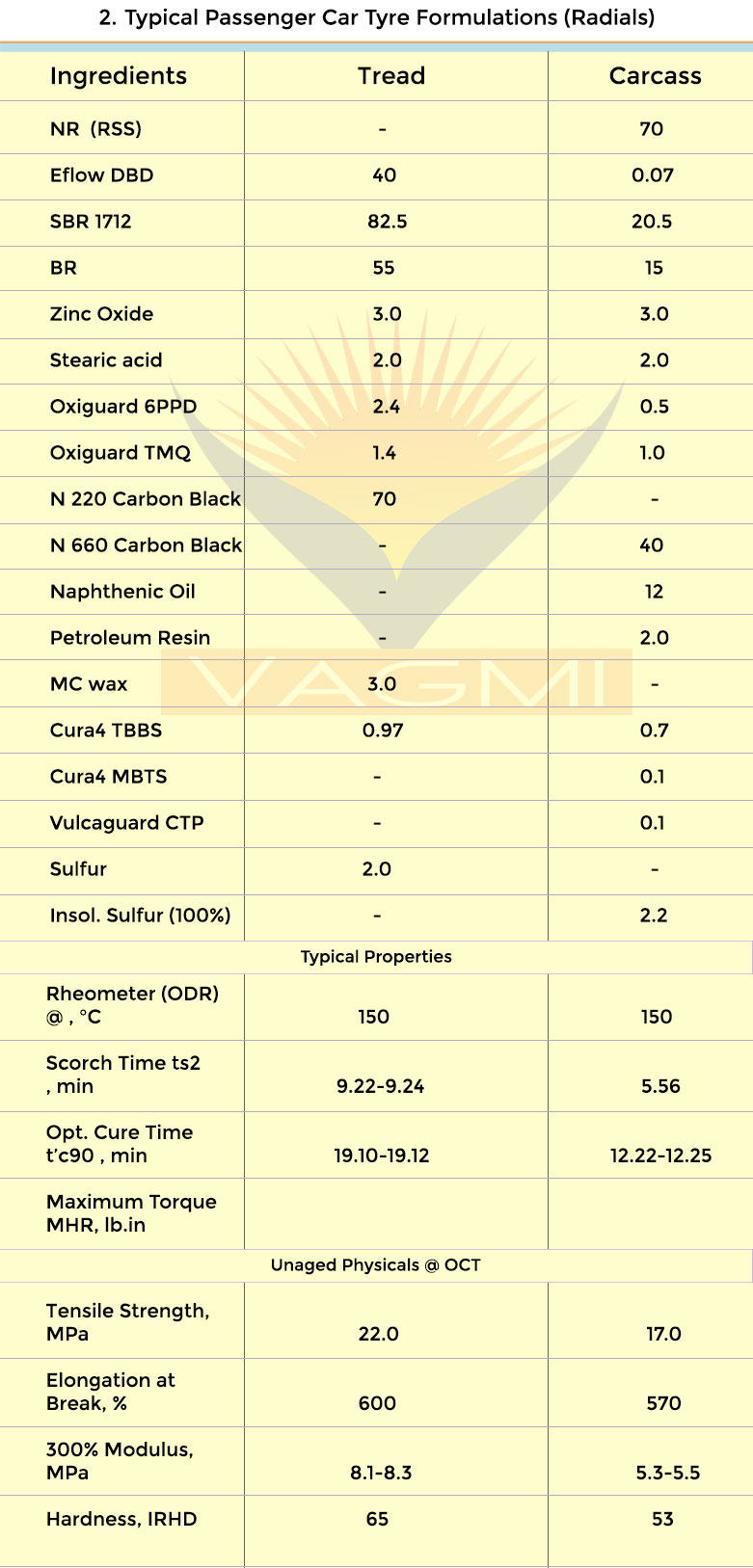
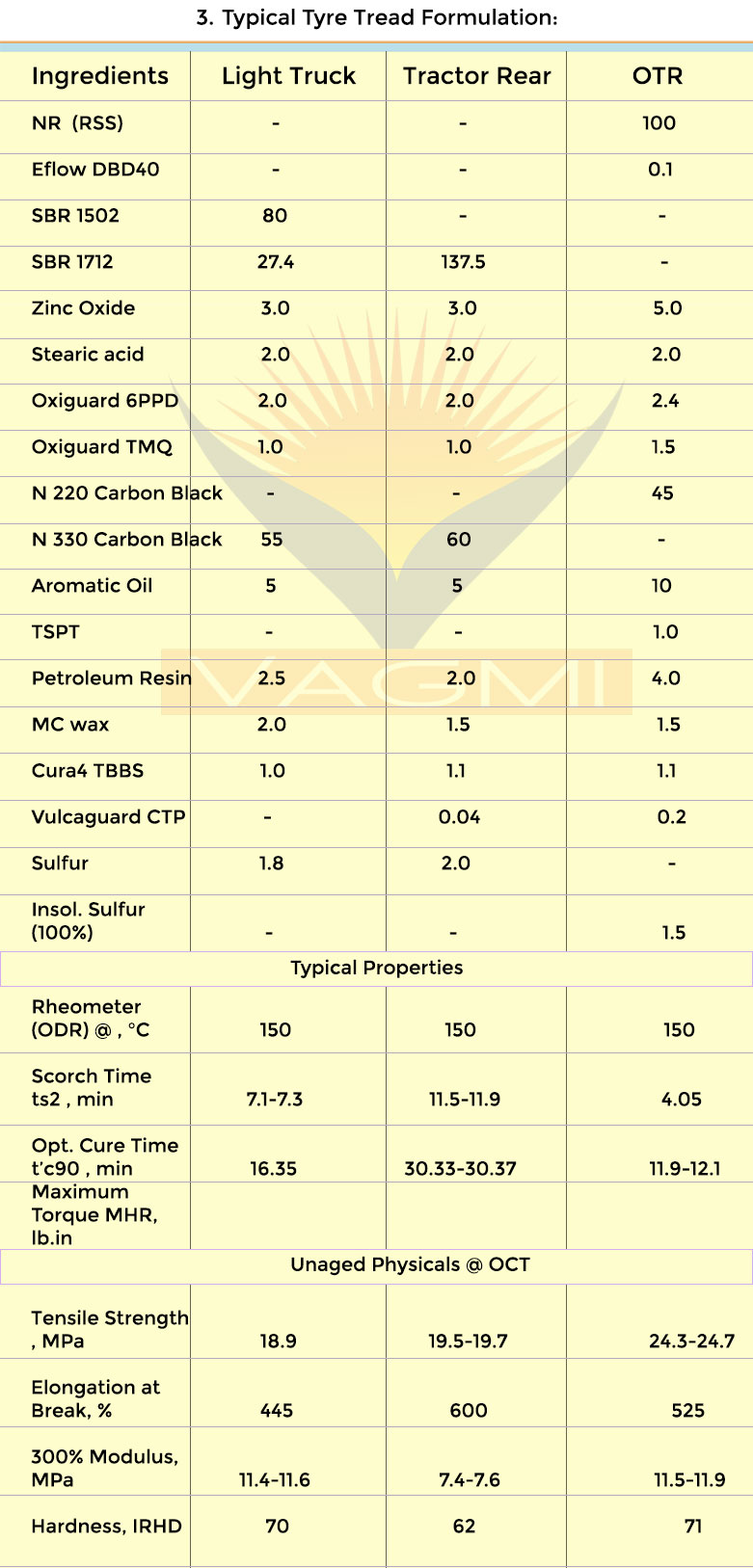
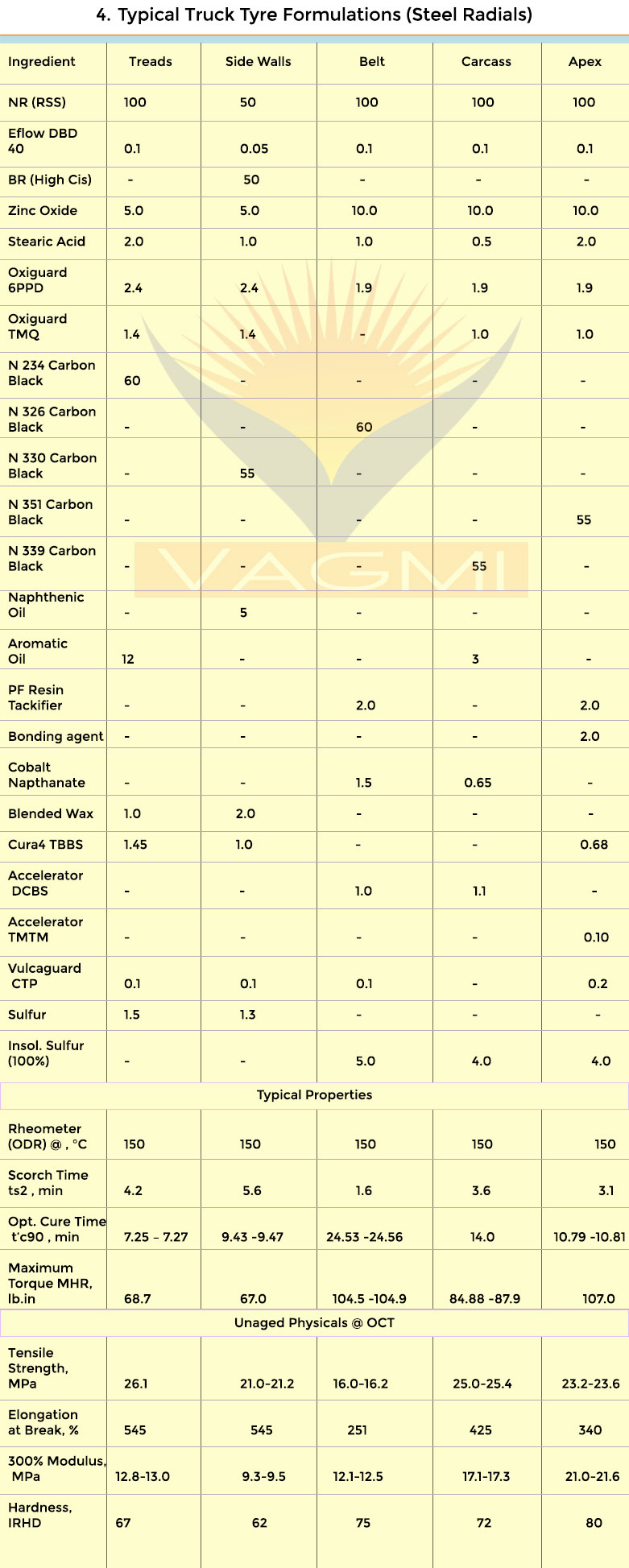
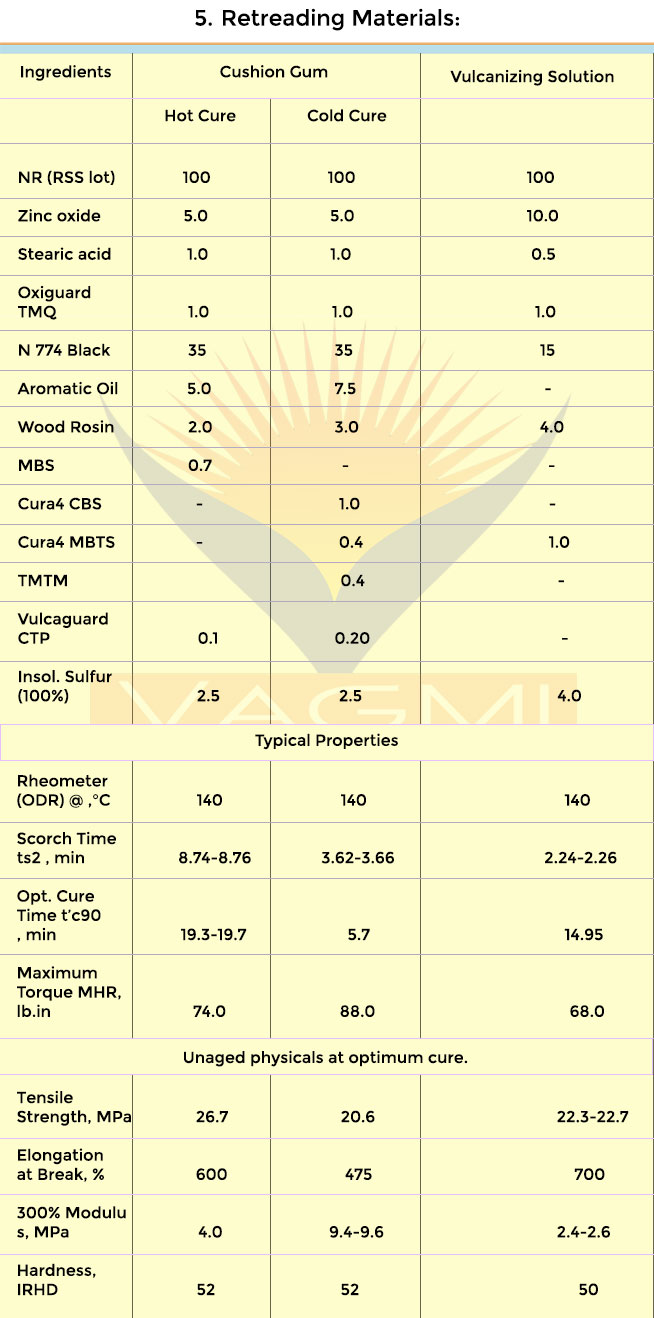
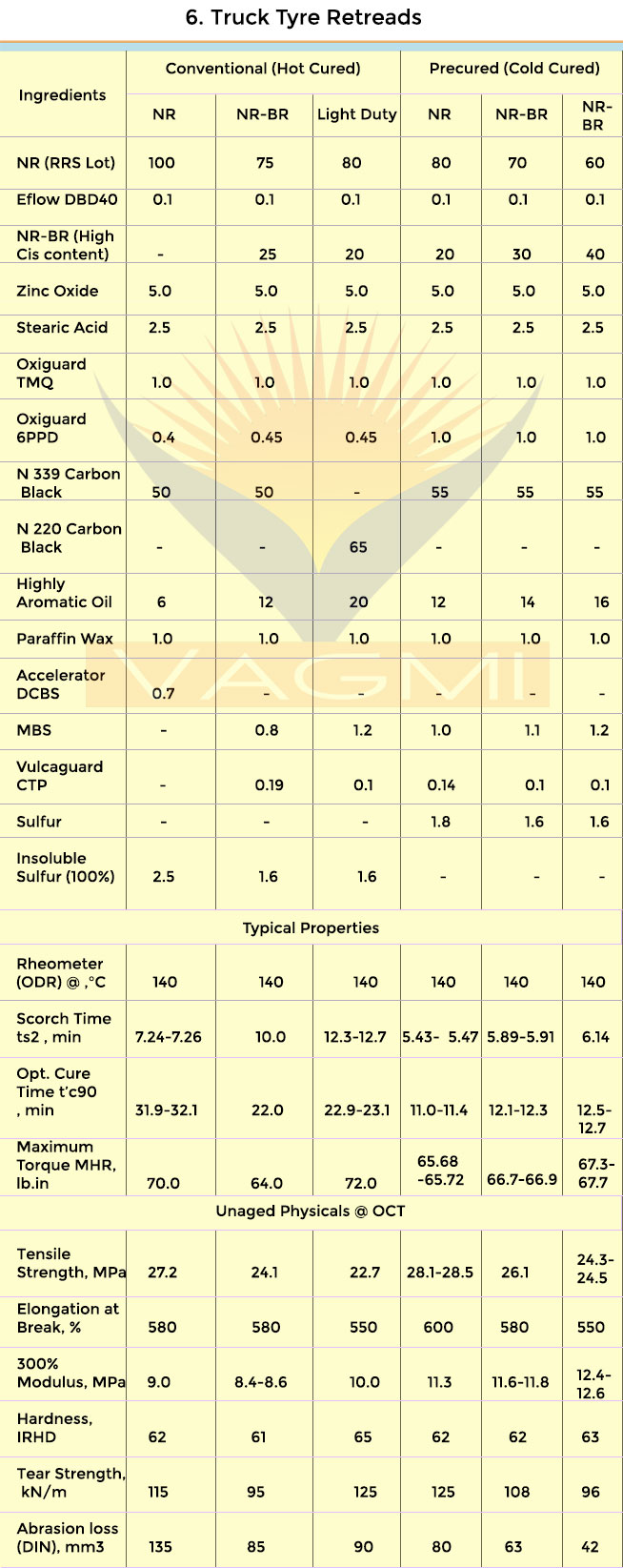
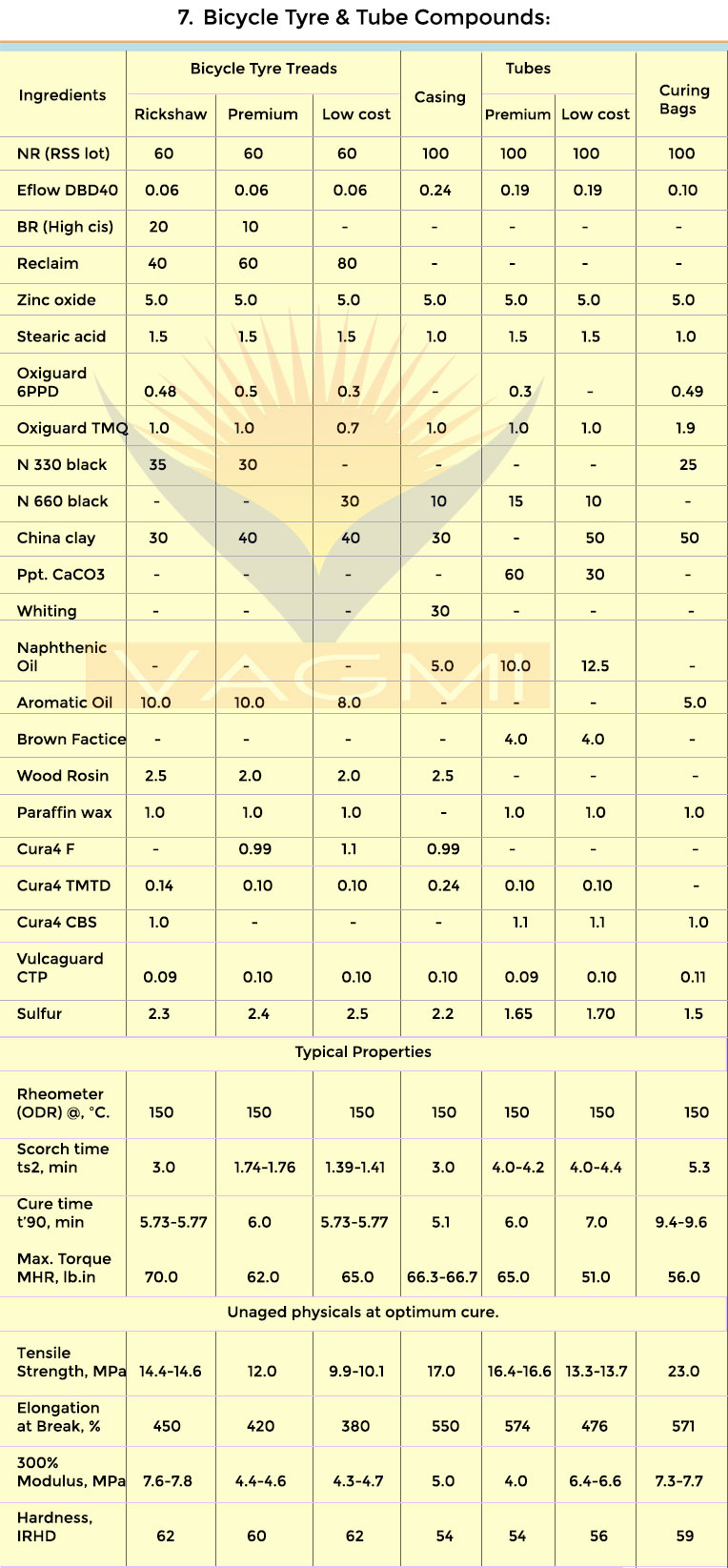
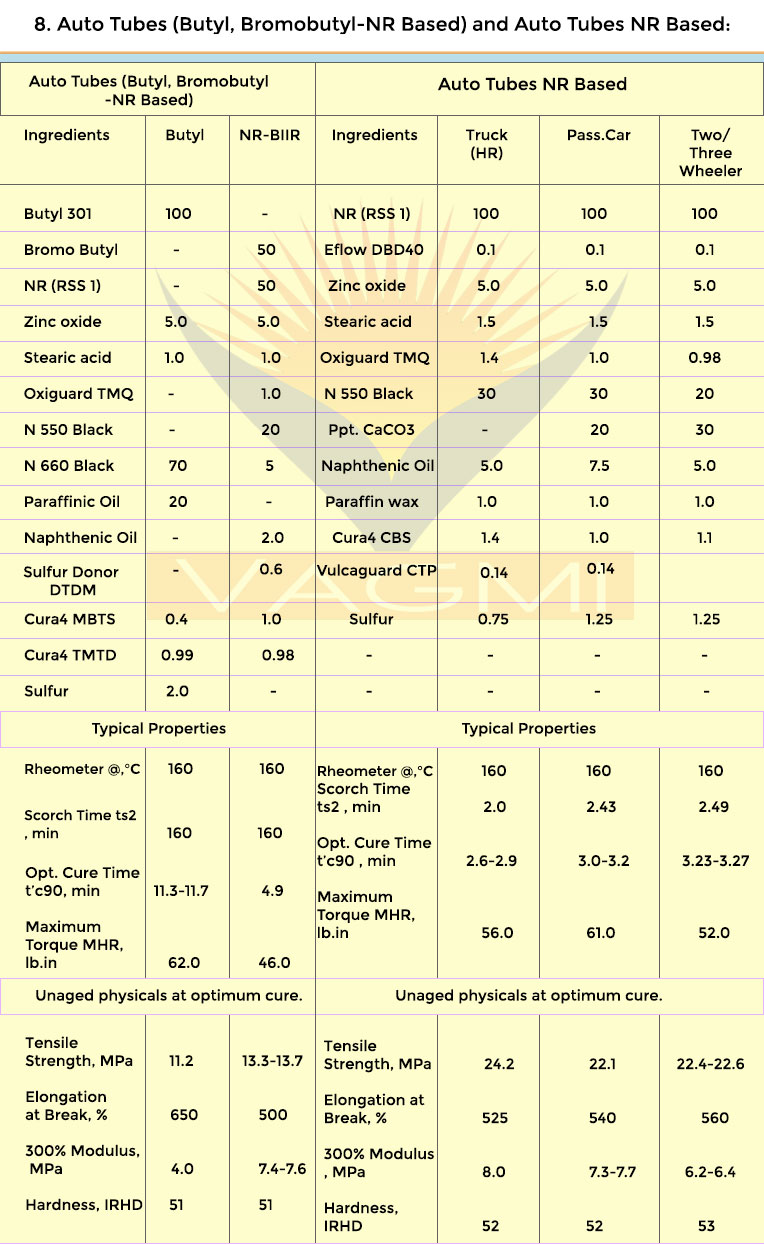
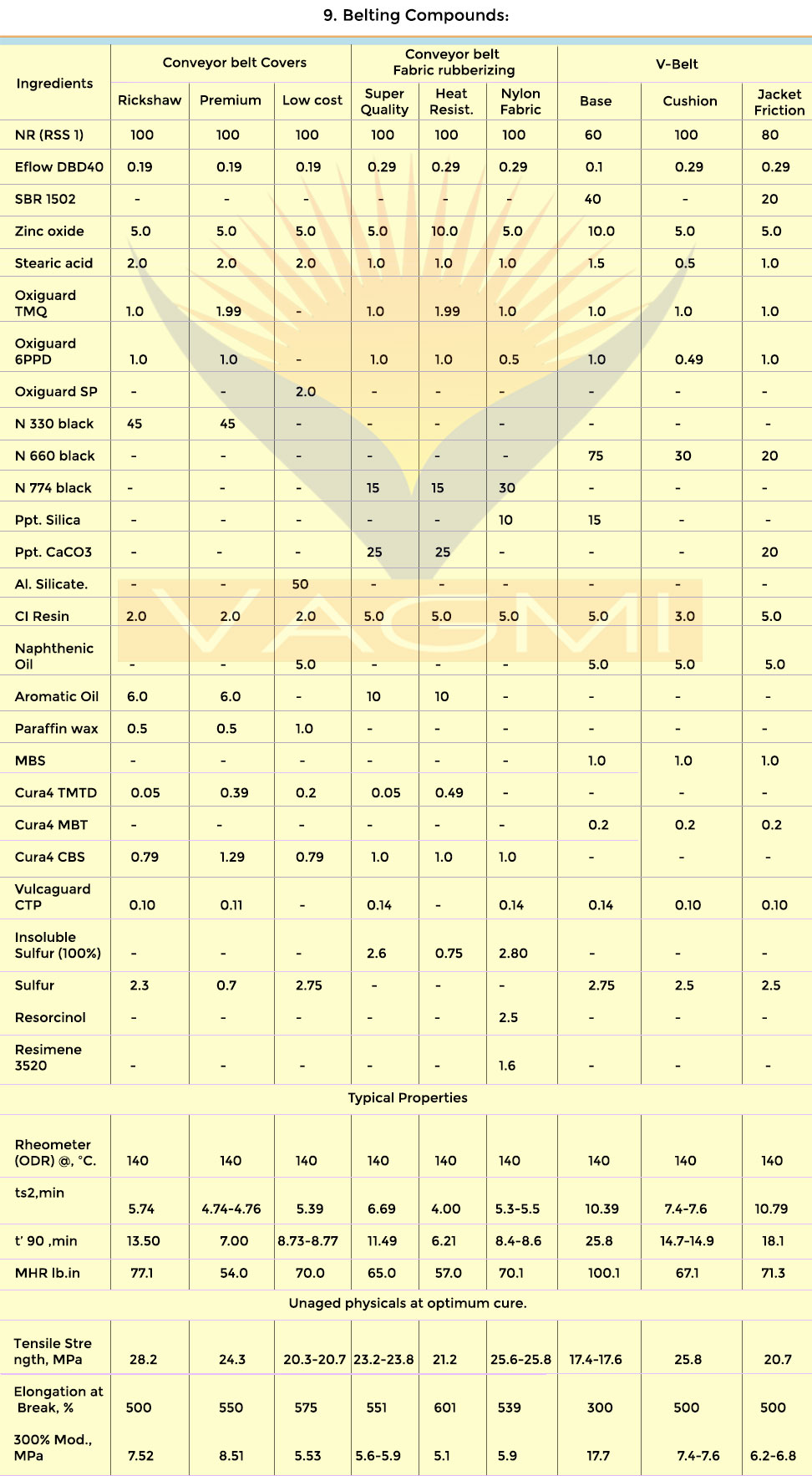
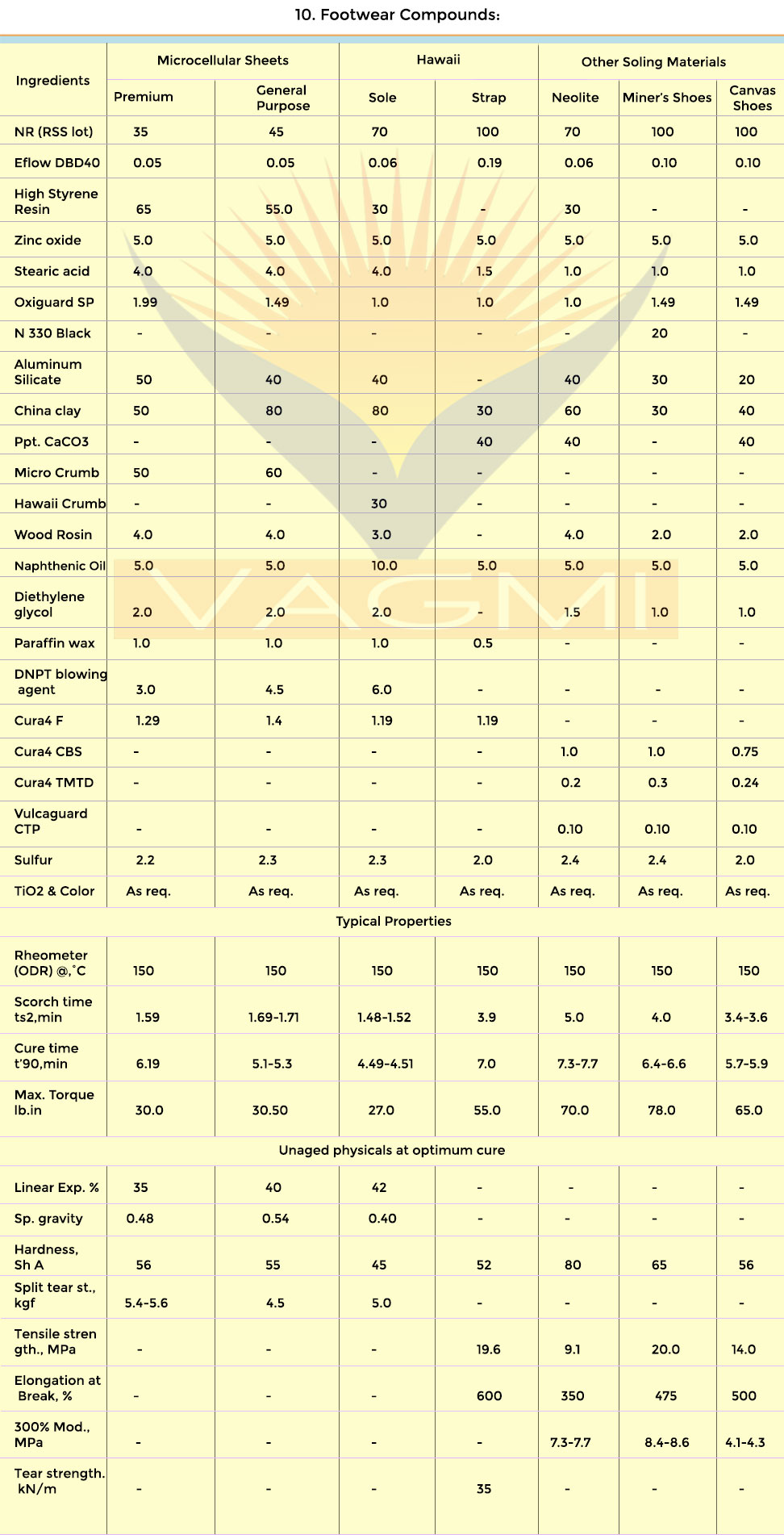

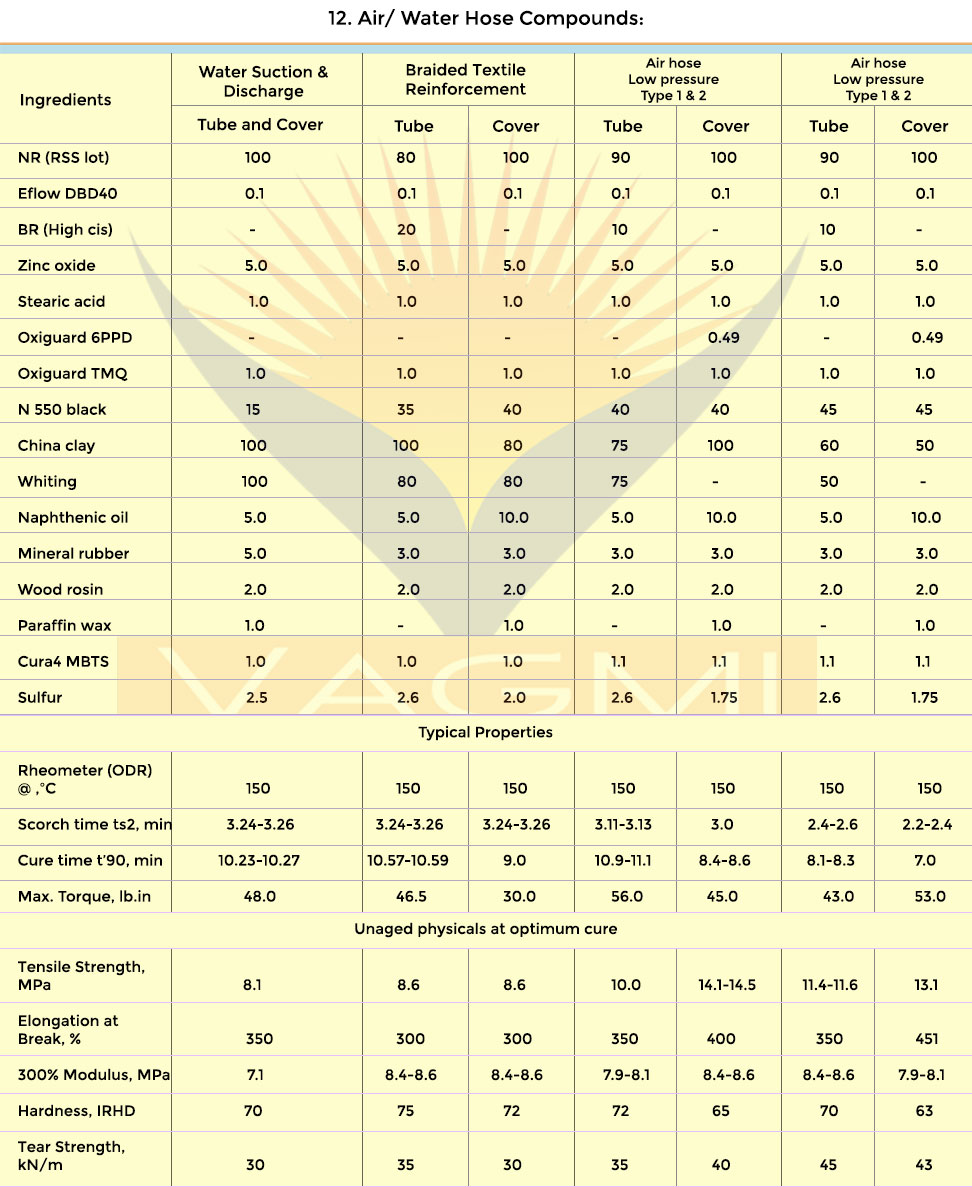
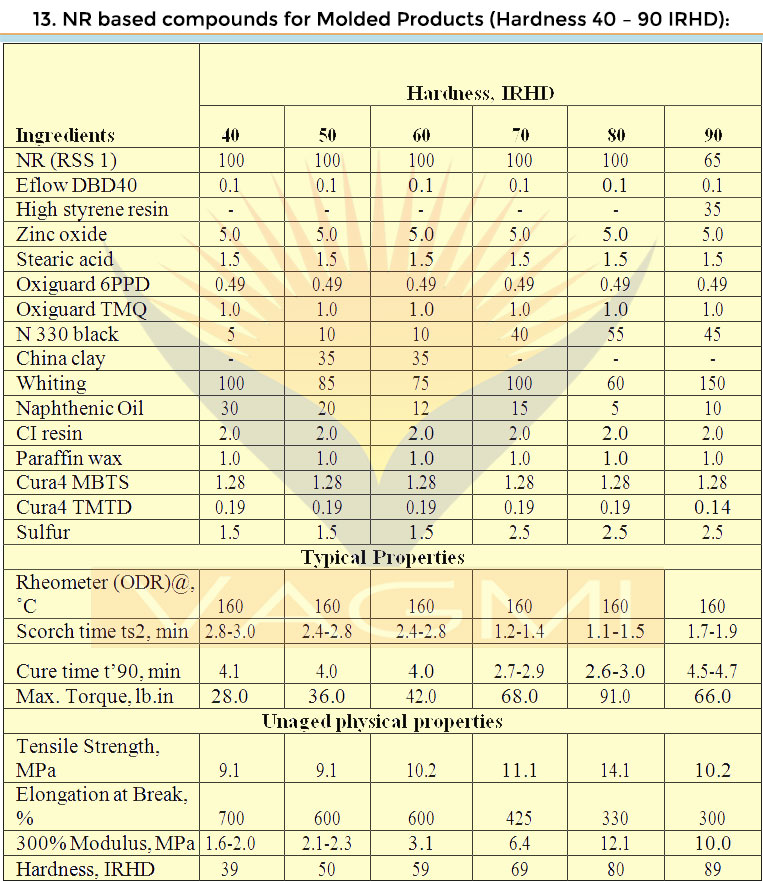



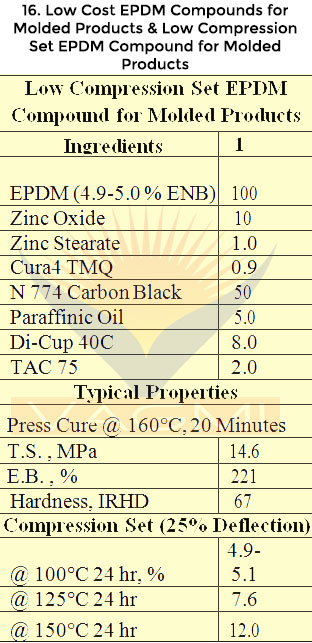




Comparative Properties of Elastomers:
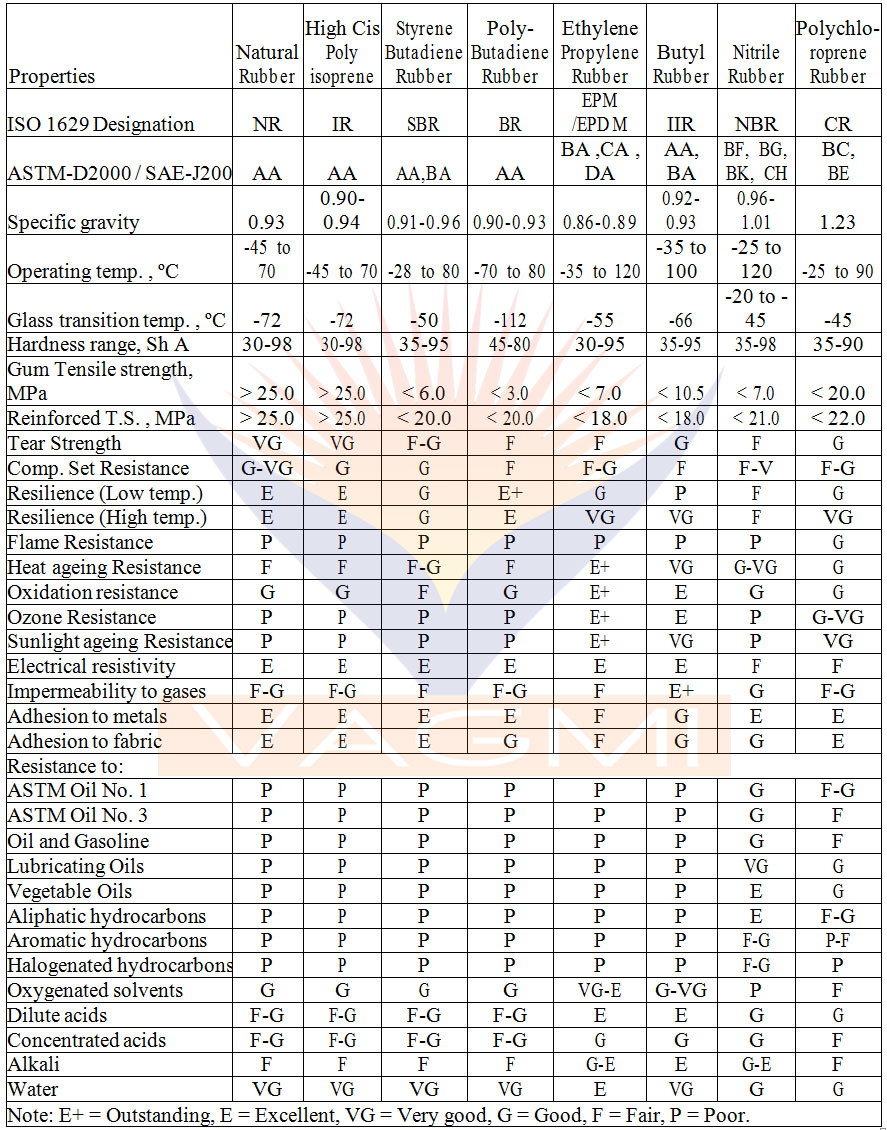

Carbon Blacks used for Rubber Compounding (Basis of classification):
The average surface area of the carbon black as measured by ‘Nitrogen surface area (NSA)’ divided into 10 arbitrary groups as follows.
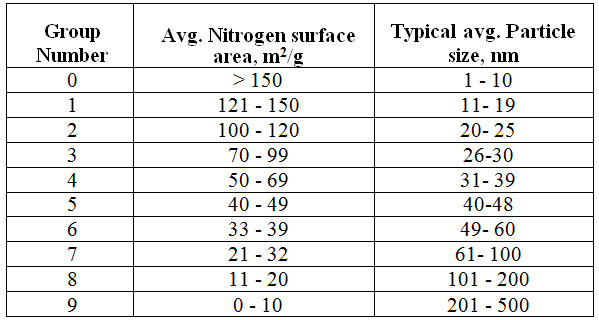
Carbon Blacks: Summary of Typical Properties:
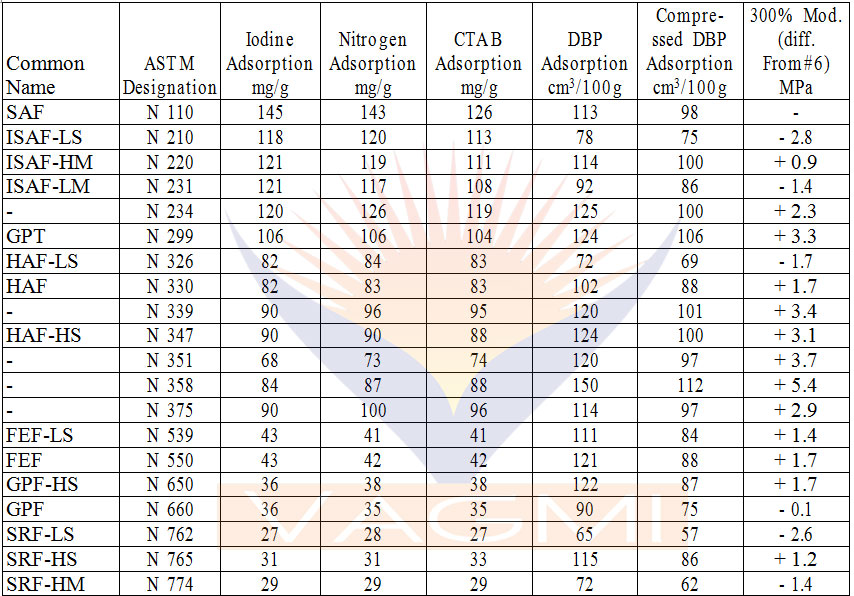
Non-Black Fillers: Summary of Typical Properties:

Effect of Fillers on Processing and Vulcanizate Properties of Rubber Compounds:
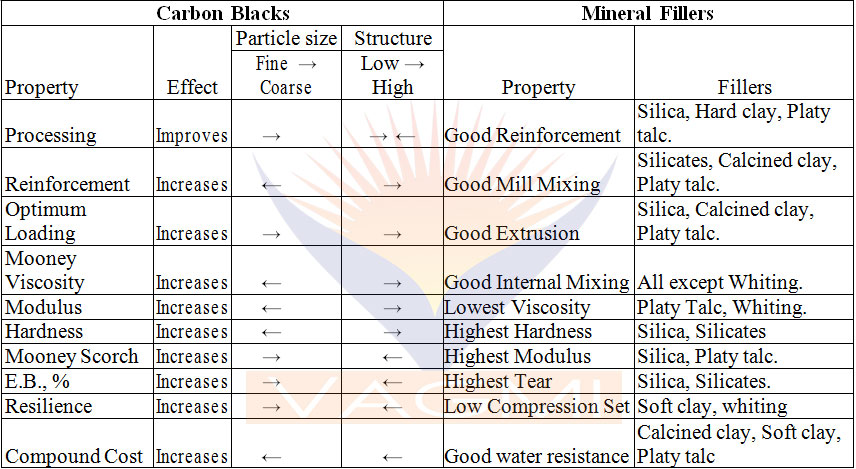
Estimation of Shore A Hardness of Rubber Compounds:
Procedure: To the base polymer hardness; add/subtract hardness change for each filler or softener.

Typical Properties of Rubber Processing Oils:
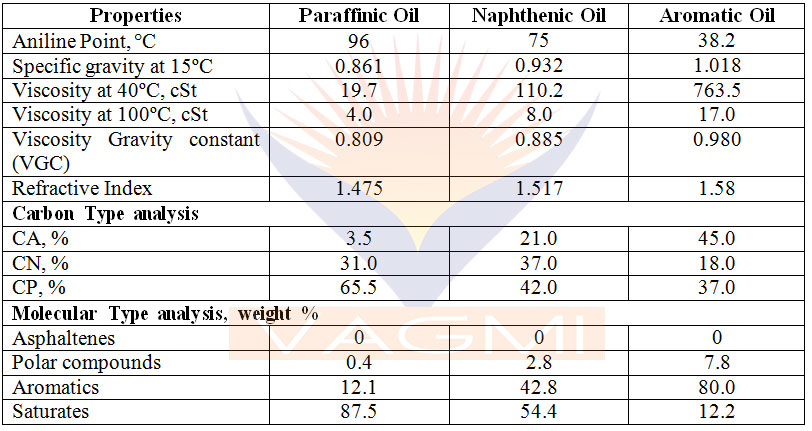
Capacities of Mixing Mills:

Capacities of Refiner Mills & Cracker Mills:
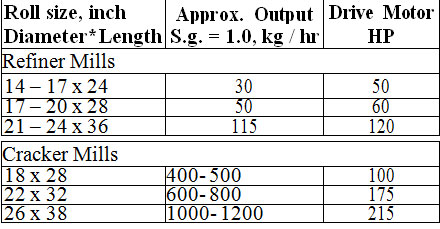
Mold Shrinkage calculations for rubber Mold Design:
%Shrinkage = [0.0205-(100-X) M] x ∆T
where,
X = Rubber Content by volume (include oil, factice etc.), ∆T = Difference between curing temperature & room temperature in ºC
M = Constant depending on filler (Usually, 0.00025 – 0.00030)
Capacities: Banbury Mixers

Typical Data: Hot Feed Extruders
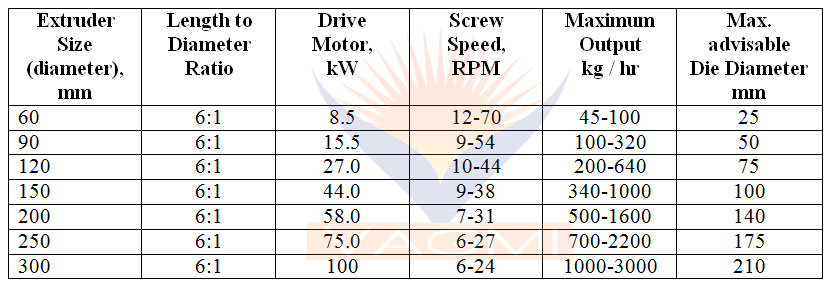
Typical Data: Cold Feed Extruders
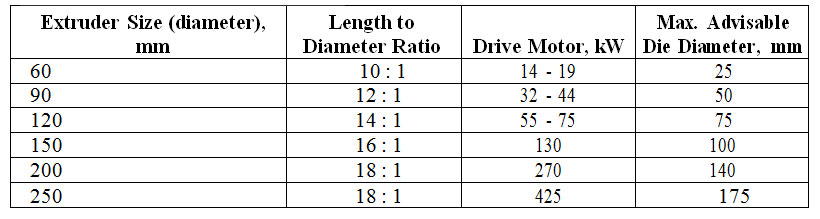
Sieve Sizes Comparison:
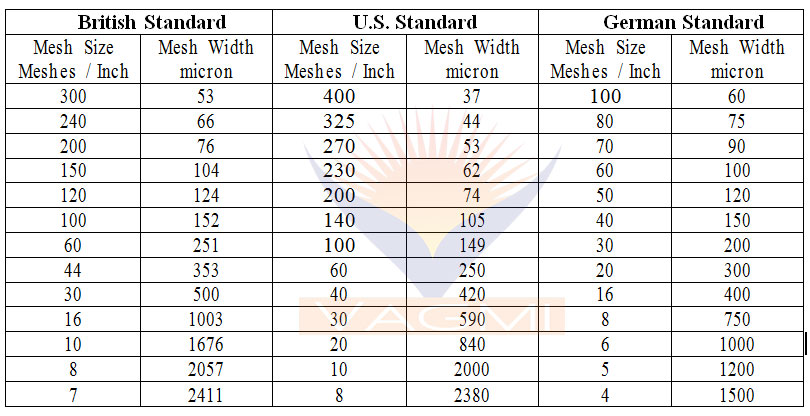
Selected Conversion Factors:

Specific Gravity of Materials:
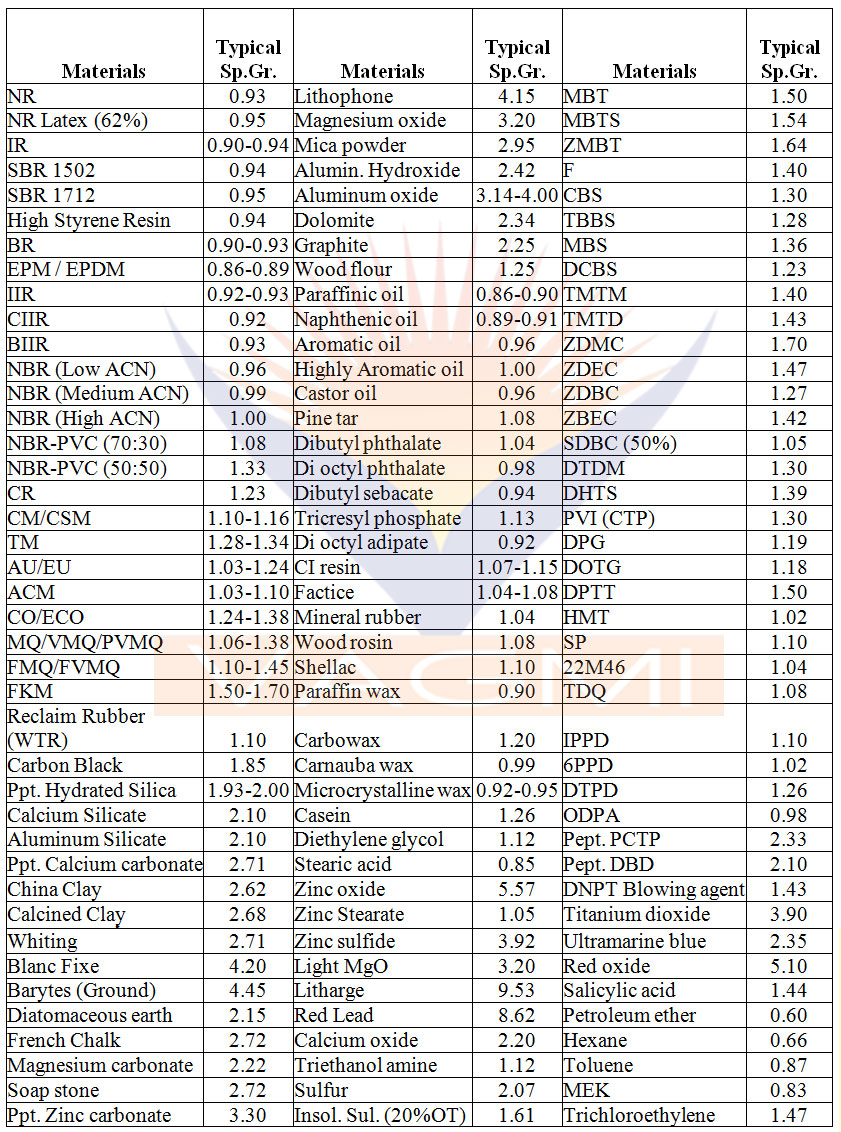