Rubbers are used for various indoor and outdoorapplications. Concerning about the outdoor application,the rubber goods should be protected from oxygen,ozone, light, and heat to extend the service lifeor prevent aging of the vulcanized rubber goods.Most natural and synthetic rubbers containing unsaturatedbackbones can be easily oxidized.In a rubber article no degradation takes place when stored in absence of air, but when they are stored in presence of air the following changes takes place may be in the form of:
Anti oxidants
Antidegradants:
Hardening, embrittlement,
Loss of resilience and strength
Different surface changes like chalking, frosting, crazing, change of colour, gloss etc.
Softening and becoming sticky
Cracking (with or without orientation)
Other changes like rotting and development of odour
Basically the ageing in the rubber article may be divided into the following processes;
Oxidation at lower or higher temperatures (ageing in the real sense)
Oxidation accelerated by metal heavy metal compounds (Rubber poison)
Effect of heat in the presence of moisture (steam ageing, hydrolysis)
Oriented crack formation by dynamic stress (fatigue)
Oriented crack formation by ozone under static &dynamic condition
Random crack formation by high energy ultraviolet light and oxygen (crazing, chalking effect)
Changes in surface frosting
Heat ageing with simultaneous exposure to swelling in chemicals
Mechanism of elastomers oxidation:
The oxidation of polymers is most commonly depicted in terms of the kinetic developed by Bolland and coworkers(J. L. Bolland, Rev. Chem. Soc. 3, 1, 1949). The scheme is summarized below. The key to the process is the initial formation of a free radical species. At high temperatures and at large shear forces, it is likely that free radical formation takes place by cleavage of carbon-carbon and carbon-hydrogen bonds.
Initiation:

Propagation:

Termination:

Bolland oxidation mechanism (RH = rubber hydrocarbon)
Many elastomers are already observed to oxidize at moderate temperatures(below 60°C), where the energetics would not favour cleavage of carbon-carbon andcarbon-hydrogen bonds. Thus, several studies have been conducted to determinewhether trace impurities present in the polymer systems could account for the relativeease of oxidation. Two separate studies concluded that traces of peroxide were presentin the polymer and that initiation occurred at low temperatures due to the relativelyeasy homolysis of these peroxides into free radicals. Due to the high reactivity offree radicals, only trace amounts of these peroxides need
to be present to provideinitiation of the oxidative chain process. On the other hand, mechanical shear duringprocessing and bale compaction and localized heat during the drying and packaging ofthe raw polymer are the most important causes of carbon-carbon and carbon-hydrogenbond cleavage. The resultant free radicals react with oxygen to form the peroxidesresponsible for degradation.
The rate of peroxide decomposition and the resultant rate of oxidation ismarkedly increased by the presence of ions of metals such as iron, copper,manganese, and cobalt. This catalytic decomposition is based on a redoxmechanism, as in figure below. Consequently, it is important to control and limit theamounts of metal impurities in raw rubber.

Decomposition of peroxides by ions of metals (Redox mechanism)
Effect of Degradation on Elastomers


Effect of Oxygen:
The absorption of only 1 to 2% by weight of oxygen can result in loss of all useful elastomeric properties.
The degradation of a polymer can be induced by light, heat, and oxygen and can be greatly accelerated by stress, presence of catalysts of oxidation, compounding formulation design and exposure to other chemicals etc.
The deterioration of the thermo-physical and mechanical properties of vulcanized diene rubbers during service is mainly caused by oxidative degradation.
The cure system selection is also influences the ageing resistance of the rubber product. Compare to the ‘Semi EV’ or ‘EV Cure’ systems, the ‘conventional Cure’ systems are more prone to oxidative degradation.
Effect of Heat:
Thermal degradation of polymers is molecular deterioration as a result of overheating. At high temperatures the components of the long chain backbone of the polymer can begin to be broken (chain scission) and react with one another to change the properties of the polymer.
The oxidative heat ageing causes loss of Tensile Strength, Elongation at Break and overall Elasticity of the rubber vulcanizates.
Natural rubber (NR), unlike many other polymers, is highly susceptible to degradation, due to the presence of double bonds in the main chain. Degradation of NR is accelerated mainly by heat.
Effect of Heat on NR Vulcanizates:

Effect of UV-Light & Weathering:
UV radiation causes photo-oxidative degradation which results in breaking of the polymer chains, produces radicals and reduces the molecular weight, causing deterioration of mechanical properties and leading to useless materials, after an unpredictable time.
Degradation process is accelerated mainly by humidity, light, ozone, and radiation etc.
When an unsaturated vulcanizate is exposed to prolonged sunlight a small amount of non-oriented cracks ca develop on the surface.
The light coloured articles on exposure to warm, moist, ozone containing atmosphere appears to be dull coloured as compared to the previous gloss than the black coloured products (as carbon black itself acts as a UV-light absorber)
The whitish surface discolouration is known as frosting.
UV-light attack is more severe in case of rubber products with a thin cross section.
Effect of Heavy Metal Ions:
Many heavy metal compounds those of copper and manganese have a catalytic action on the oxidation of rubber blends and vulcanisates.
Reaction is especially sensitive to copper: degradation is sufficiently promoted to warrant description as “copper attack”, having a major impact on the polymer.
When an unsaturated vulcanizate is exposed to prolonged sunlight a small amount of non-oriented cracks ca develop on the surface.
The order of effect of different metal elements on polymers is as follows:
Co > Mn > Cu > Fe > V >> Ni > Ti = Ca = Ag = Zn > Al > Mg
In particular even traces of e.g. 0.001 wt% of Cu and Mn compounds in NR are able to accelerate the auto-oxidation of the rubber and the vulcanisate and hence they are called rubber poison.
The general decomposition mechanism of the rubber soluble heavy metallic compounds catalyze hydro-peroxide to free radicals

Besides these rubber poisons other heavy metal compounds like Fe++ especially poisonous in SBR. Cobalt and nickel compounds also accelerate ageing phenomena.
In general standard antioxidants do not give protection against heavy metal ions. It is possible to protect the stock by incorporating substances which react with the metal ion to give stable coordination complex.
Effect of Dynamic Fatigue:
When a rubber article is subjected to prolonged mechanical stress, the article periodically bends back and forth, cracks will slowly develop in the surface and they will grow and leads to the breakage of the article.
The fatigue crack resistance not only depend on the type of rubber but also on the crosslink density and type of crosslinks (higher crosslink density and sulfur rich crosslink structures are preferred).
NR vulcanisates form these cracks relatively quickly but they grow slowly. SBR shows slower start of crack but once the cracks are formed they grow faster. This is connected to the low tear resistance to the SBR vulcanisates.
The fatigue failure is initiated at minute flaws where stresses are high and mechanical rupture at such points can lead to developments of crack. The cracks develop perpendicular to the stress direction.
Higher temperature and higher frequency of stress change accelerate crack formation. If higher ozone concentrations are also present dynamic crack formation is accelerated.
Effect of Ozone:
Ozone is generated naturally by electrical discharge and also by solar radiation in the stratosphere.
Formation of O3 requires the high energy carried by wavelengths of less than 240 nm; only then does O2 dissociate to monatomic oxygen, which binds immediately with O2 present in the vicinity to form O3.
More recently, because a gas mixture of oxygen plus the NOx and hydrocarbons discharged from motor vehicles is converted to ozone by short wavelengths (300 nm or less) even in the weak ultraviolet reaching the ground, the converse is happening and ozone is being evolved at high concentration in conurbations where NOx is abundant.

Shows the ozone generation mechanism for exhaust gas from urban vehicles
Since ozone is very highly oxidising, it had been presumed that this ozone, which oxidises dust and other pollutants, is immediately consumed in polluted areas of intense urban activity; thus, while the ozone level was high along the coast and in the mountains where the air is clean, almost no ozone could be found in cities.
In the presence of longer wave length UV light, nitrogen dioxide dissociated as nitrogen oxide (NO) and monatomic oxygen (O).
The Oxygen atoms then combine with Oxygen molecules present in the atmosphere to form Ozone.
The Action of Ozone on Diene Rubbers and the Crack Initiation Mechanism
Ozone attacks the double bond to produce an ozonide, which is unstable and cleaved at the O-O linkage, with formation of a zwitterion. Aldehyde or ketone is also formed. The intermediate products are stabilised by four routes [Murakami, K.: “Gomu no Rekka Rouka Hakai to sono Boushi”, Keieikaihatusyuppanbu, Tokyo, p.308 (1980)]. As to the mechanism of ozone cracking initiation, on the other hand, opinions diverge. Generally speaking, a vulcanised rubber surface contains numerous minute flaws and irregularities in profile which are enlarged by elongation of the rubber. Ozone also has a great effect when residual stresses from forming and processing persist within the rubber. When the rubber is under elongation,
the amount of ozone penetrating and rate of permeation-diffusion are large compared with the unstretched rubber; the ozone can then attack the double bonds in the defects directly, facilitating crack initiation. If the breaks in the molecular chain then recombine, crosslinking occurs and the polymer stabilises. Hence, if rubber is left in a high concentration ozone atmosphere in an un-stretched state with the molecular chains un-oriented, the surface hardens as a result of crosslinking; the material then feels solid to the touch, but since ozonolysis is a surface reaction and hardening is limited to the extreme outer surface, countless cracks develop the instant the slightest of stresses is applied.
Thus, the outer surface and interior will present completely different rubbery states. Inspection of appearance to identify microcrack initiation is a technique much used for routine appraisal of ozonolysis, but ozonolysis is in fact very diffi cult to appraise by observation since it coexists with fatigue (in which microcracks develop as in ozonolysis) and ordinary oxidative degradation.

Ozone attacks the double bonds to produce an ozonide (I). (I) is unstable and its O-O bond breaks, giving rise to a zwitterion (II). Also formed are the zwitterion (III) and an aldehyde or ketone (IV).
The intermediate product (III) is stabilised via the four different routes shown below.
recombines with aldehyde to form the stable ozonide

Stabilisation by formation of a polymerisable peroxide

Hydroperoxide is formed by reaction with a solvent containing active hydrogen

Rearrangement occurs, with formation of esters, lactones, anhydrides and acids.
Role of Antidegradants:
Antioxidants and antiozonants act either by interrupting chain reactions or by preventing free-radical function and protect the polymer during processing and protect the finished product.
Antidegradants rank second after vulcanizing agents as the most important ingredients in rubber compounding without which the final product would have an extremely short life span and have a dramatic impact on the service life of the rubber product although being present at extremely low concentrations (0.5 – 3.5 phr).
Once compounded into the rubber during mixing, the antidegradant is expected to fulfil its role of protecting the product from premature ageing through a specific mechanism depending on its chemical nature and environmental conditions under which the product has to operate.
The effectiveness of an antidegradant can therefore be assessed by the length of time the product remains useful in what it was designed to do.
Important characteristics of Antidegradants:
The important characteristics of antidegradants can be summarized as follows:
Discoloration and staining:
In general, phenolic antioxidants tend to be non-discolouring and amines are discolouring. Thus for elastomers containing carbon black, more active amine antioxidants are preferred since discoloration is not important.
Volatility:
As a rule, the higher the molecular weight of the antioxidant, the less volatile it will be, though hindered phenols tend to be highly volatile compared with amines of equivalent molecular weight. Thus, correct addition of antioxidants in the compound mix cycle is critical if loss of material is to be avoided.
Solubility:
Low solubility of an antidegradant will cause the material to bloom to the surface, with consequent loss of protection of the product. Therefore, solubility of antidegradants, particularly antiozonants, controls their effectiveness. The materials must be soluble up to 2.0 phr and must be able to migrate to the surface.
Chemical stability:
Antidegradant stability against heat, light, oxygen, and solvents is required for durability.
Concentration:
Most antidegradants have an optimum concentration for maximum effectiveness after which the material solubility becomes a limiting factor. para-Phenylenediamines offer good oxidation resistance at a loading of 0.5–1.0 phr and antiozonant protection in the range of 2.0–5.0 phr. Above 5.0 phr para-phenylenediamines tend to bloom.
Environment, health, and safety:
For ease of handling and avoidance of dust and inhalation, antidegradants should be dust-free while free flowing. While selecting antidegradant for products coming in contact with food or in pharmaceutical use, one must be confirm the suitability of the antidegradant.
Economics:
Cost of overall the antidegradant system is the most important factor. The antioxidants are selected after considering the total service life expected from the product itself.
Classification of Antidegradants:
Antioxidants
Antiozonants
Antioxidants:-
those antidegradants that give protection against ageing caused by oxygen, steam and light.
Classification of Antioxidant:
There are two basic classes of antioxidant:
Amine type: generally more powerful but staining
Phenol type: non-staining
Amine Type Antioxidant:
The amine antioxidant may be subdivided into the following groups:
Phenylnaphthylamine:
At one time the phenylnaphthylamines, particularly phenyl-β-naphthyl-amine (PBN) were the most important commercial antioxidants.
Ketone-amine condensates:
The ketone-amines, on the other hand, remain one of the two major classes of commercial antioxidant offering very good heat resistance to diene rubbers and in some cases very good flex cracking resistance. So they are mainly used in tyre, cables and heavy-duty mechanical goods where heat resistance is an important requirement.
Substituted diphenylamines and p-phenylene diamines:
The di-substituted p-phenylene diamines are very commercially important. Di-aryl compounds such as di-β-naphthyl-p-phenylene diamine confer very good heat resistance and metal inhibition but the specific antioxidant. When antioxidants are often used in combination then they perform the variety of role as antidegradants. For example, the dihydroquinoline derivatives with their particularly good long term heat resistance are mainly used in conjunction with the p-phenylene diamines in tyre compounding.
Comparison of amine antioxidants:

Phenol type Antioxidant:
For marginal of rubber applications it is important that additives should not discolour or cause staining through migration. It is this requirement which has led to the use of phenolic antioxidants. They also find additional use as stabilizers for raw polymer to improve stability before compounding and in formulations where toxicity is a consideration.
There are two main classes:
Simple hindered phenols also known as mononuclear phenols or as monohydric phenols of general type

Bridged hindered phenols or polynuclear phenols. In turn these may be subdivided into:
Bisphenols of the phenyl alkane type:

Bisphenols of the phenolic sulphide type:

Polyphenols type:

Some simple phenols can show very good protection against light and flex cracking. The substituent groups are of electron releasing type in order to increase the antioxidant efficiency. For example 2,6-di-t-butyl-4methylphenol is 100times more effective as antioxidant in petrol than phenol itself. These monohydric phenols are widely used for polymer stabilization. But in case of bridged hindered phenol antioxidants, the activity of this type of antioxidant depends on the nature and position of the bridge. In rubber vulcanizates, the best results are usually obtained with an ortho bridge. In the case of phenol alkanes, the highest activity is obtained with methane. The phenolic sulphides are not practically powerful and do cause some discolouration. In rubbers their main use in latex compounding. As the bisphenols, the higher molecular weight polynuclear phenols have similar antioxidant activity but lower volatility.
Comparison of phenolic antioxidants:

Antiozonants:-
those that protect the rubber from cracking as a result of ozone attack.
The following observations were extensively studied of substituted p-phenylene diamines which act as antiozonants in 1963 (Ambelang et al.)
Ring-substituted p-phenylene diamines (ppds) were less effective than unsubstituted ppds.
The effectiveness as an antiozonant decreases in the sequence para > ortho > meta.
An increase in the number of rings between –NH- groups reduced the effectiveness
In the case of alkyl-subtituted compounds, the secondary alkyls appear the most effective.
There are three types of p-phenylene diamines:
Diaryl ppds
Dialkyl or cycloalkyl ppds
Aryl-alkyl ppds
The diaryl ppds show either poor compatibility or poor antiozonant activity or both in diene hydrocarbon rubbers. But in case of polychloroprenes, N-N’- ditolyl-p-phenylne diamine (DTPD) is used as antiozonant. The dialkyl ppds confer the best antiozonant to diene hydrocarbon rubbers at static condition. The most common dialkyl ppds are N,N’-dicyclohexyl-p-phenylenediamine (DCPD) and N,N’-bis(1,4-dimethylpentyl)-p-phenylenediamine [B(DMP)PD]. Under dynamic condition the most common aryl-alkyl ppds are N-isopropyl-N’-phenyl-p-phenylenediamine (IPPD) and N-1,3-dimethylbutyl-N’-phenyl-p-phenylenediamine (6PPD).
Chemical name of some commercially available antidegradants:
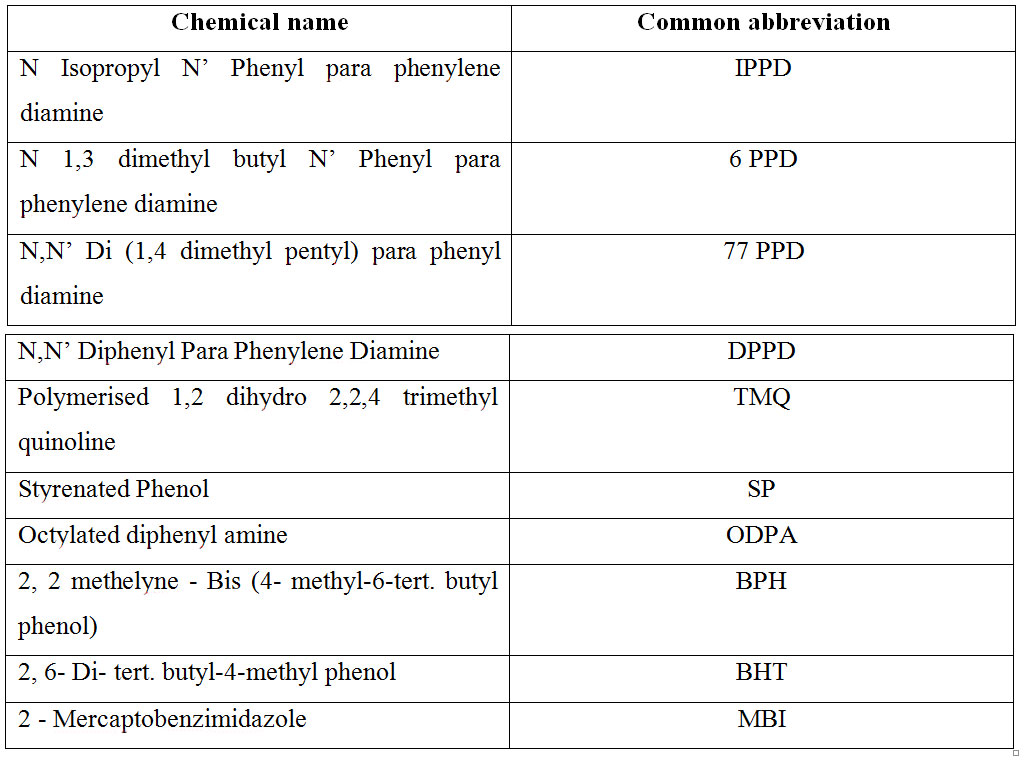
Activity of antidegradants:
General mechanism of protection:
There are three broad classes of antioxidants which are recognized as being able to inhibit the oxidation process at the points shown below:

General antioxidant mechanism of protection
Paraphenylene diamines (PPDs):
The general chemical structure of PPDs can be represented as follows:

Diaryl ppds:
This class of PPDs generally contains two aromatic pendant groups, as in diphenyl-p-phenylenediamine or di–naphthyl-p-phenylenediamine. They are less active than alkyl-aryl PPDs and tend to bloom, thus rendering them unsuitable for many applications. The general and most common chemical structure of N,N’-Diaryl-p-phenylenediamine can be represented as follows:

Dialkyl PPDs
The substituent R groups are both alkyls, as in diisopropyl-p-phenylenediamine. The R group can range from C3 up to C9. Dialkyl PPD antidegradants tend to induce higher levels of scorch in a compound than other classes of PPD antidegradants, and tend to migrate faster than other PPD because of their low molecular weight.

N,N’-bis (1,4-dimethylpentyl)-p-phenylenediamine (77PD)

N,N’-dioctyl-p-phenylenediamine (88PD)
Alkyl-aryl PPDs
One R group is an aromatic ring and the other is an alkyl group. The most widely used PPD in this class is N-1,3-dimethylbutyl-N′-phenyl-p-phenylenediamine. This antiozonant offers good dynamic protection, good static protection when combined with wax; better compound processing safety and scorch safety, and slower migratory properties, allowing it to be more suitable for long product life.

N-isopropyl-N’-phenyl-p-phenylenediamine (IPPD)

N-1,3-dimethylbutyl-N’-phenyl-p-phenylenediamine (6PPD)

Action as antidegradant:
N,N’-substituted p-phenylenediamines (PPDs):
The most widely used antioxidants in the rubber industry are N,N’-substituted p-phenylenediamines (PPDs) [Cataldo F, Eur Polym Journal, 38, 885, 2002], being effective also as antiozonants with anti-fatigue effects. The mechanism of inhibition by phenylenediamines is given below:

The mechanism of inhibition effect of PPDs
Benzoquinone diimines (BQDI) were isolated as reaction products of the first step. As seen from the above reaction mechanism, their chemistry involves condensation, hydrolytic and redox reactions. Compounds with benzoquinone monoimine (BQMI) structures and N-heterocyclic compounds are formed and the structure of substituted phenylenediamines is regenerated. BQDI are able to trap R• radicals. This contributes to the antioxidant efficiency of the originally added phenylenediamine derivative due to the regeneration of the ROO• trapping species [Z. Cibulkova´ et al., Polymer Degradation and Stability, 87, 479-486, 2005].
Protection against Ozone by Substituted PPDs:
The most effective antiozonants are the substituted PPDs. Their mechanism of protection against ozone is based on the ‘scavenger-protective film’ mechanism [R. P. Latimer, E. R. Hooser, R. W. Layer, C. K. Rhee, RUBBER CHEM. TECHNOL. 53, 1170, 1980]. The reaction of ozone with the antiozonant is much faster than the reaction with the carbon-carbon double bonds of the rubber on the rubber surface [F. Cataldo, Polym. Degrad. Stab., 72, 287, 2001]. A simplified reaction mechanism for the aryl-alkyl PPDs such as 6PPD is depicted in below [K. W. Ho, J. Polym. Sci., A. Polym. Chem. 24, 2467, 1986].

Trimethyl-Dihydroquinolines (TMQs):
-
One of the most effective, peroxide-compatible primary antioxidant is TMQ.
Antioxidant TMQ (2,2,4-trimethyl-1,2-dihydroquinoline) with molecular formula (C12H15)n is a ketone amine antioxidant.
Antioxidant TMQ (2,2,4-trimethyl-1,2-dihydroquinoline) with molecular formula (C12H15)n is a ketone amine antioxidant.
It is a hindered amine (quinoline type) with a high molecular weight, low volatility, and economical price.
Because of relatively low price and great ease of application, this antioxidant is considered as a very effective and important antioxidant in rubber technologies.
It also has a metal- deactivating effect, able to chelate transition metal prooxidants such as copper, iron, manganese, chromium, and cobalt that can catalytically decompose hydroperoxides into radicals that accelerate oxidation.
It is mainly used for natural rubber and chloroprene rubber etc.
TMQ is generally limited to black compounds since it is somewhat discoloring and staining
Due to Very high activity; TMQ is effective even at lower dosages.
Generally TMQ is used at 1 to 3 phr in rubber based products.
Reaction mechanism of TMQ as antioxidant:
TMQs act as alkyl radical (R.) scavenger which immediately stops auto-oxidation process.

Use of Waxes and Saturated Polymers for Ozone Protection:
Waxes have been used for over a century to protect diene rubbers from ozone. Generally two types of wax are used to protect rubber against ozone (F.Cataldo, Polymer Degradation and Stability, 72, 287-296, 2001).
-
Paraffinic wax: mainly constituted by straight chain hydrocarbons of relatively low molecular weight about 350-420.
Microcrystalline wax: generally obtained from higher molecular weight petroleum residuals and have higher molecular weight than paraffinic was about 490-800.
This is brought about by the diffusion of the crystalline wax which has limited compatibility with the polymer onto the surface to form a protective layer not susceptible to ozone attack and effectively impervious to ozone. Pure paraffinic wax is not satisfactory as it blooms too rapidly and flakes off the rubber surface. On the other hand, many microcrystalline waxes bloom too slowly and take unduly long to become effective, so that today combinations of waxes are frequently used. The paraffinic waxes create a surface layer on the rubber which is a physical barrier to ozone attack on the diene rubber double bonds.
The Role Waxes:
-
A wax protects by blooming to the surface to form a film of the hydrocarbon which is impervious to ozone
Protection is achieved only when the film is thick enough.
Thicker films ensure better protection.
Only small molecules can migrate at lower temperatures less than 40°C.
Blooms occur whenever the solubility of the wax in rubber is reduced. The bloom and thickness of the film are increases as the solubility of the waxes decreases with reducing the temperature.
Microcrystalline waxes perform better at higher temperature. Science their mobility increases with increasing the temperature, the rate of migration to the surface is also increases. With microcrystalline wax, the maximum film bloom thickness is achieved at 50-60°C
With paraffin wax the maximum film bloom thickness is achieved at 20°C.
The high solubility of the paraffin waxes becomes a disadvantage as the temperature increases. Then they become too soluble in the rubber matrix and do not form a thick enough protective film.
Under static conditions the combination of wax with small amount of a chemical antiozonant, results in a synergistic effect in ozone resistace. This system has been attributed to the ability of the chemical antiozonant to increase the thickness of the wax bloom.
Typical properties of the different waxes:
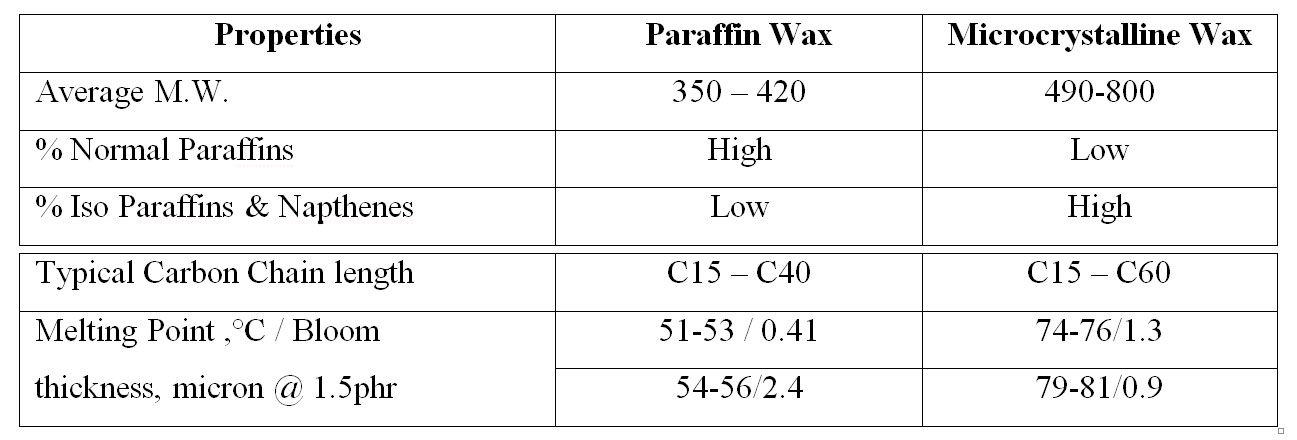
Application of different Antidegradants:
Following points must be taken into consideration before using an antidegradant :
Which rubber is involved?
-
Rubbers having fairly good amount of unsaturations like NR, IR, SBR, BR, and NBR: Mainly use IPPD, 6PPD, 77PD, DPPD, TMQ.
Rubber with low unsaturation (EPDM, IIR, partially unsaturated HNBR): TMQ, Octylated diphenyl amine (ODPA) and 2 – Mercaptobenzimidazole (MBI).
For polychloroprene rubber (CR): ODPA, MBI acts as an accelerator for CR
Is freedom from staining or contact staining demanded?
Products that stain heavily are the Paraphenylene diamine types, the nonstaining types are BHT and SP types.
What parts does anaerobic (non-oxidative) ageing play?
Antidegradants do not protect from heat as such. Special vulcanisation systems are required here especially low sulfur systems, use of thiurams, peroxides etc.
Is resistance to hydrolysis possibly required in addition to resistance to oxidative degradation?
MBI and MMBI have given good results in steam aging of diene rubbers.
What must be protected?
Surface effects (Cracking, chalking, embrittlement) or Bulk effects (Hardening, softening, loss of strength.
Food and drug application:
N Isopropyl N’ Phenyl para phenylene diamine (IPPD); N,N’ Diphenyl Para Phenylene Diamine (DPPD); Octylated diphenyl amine (ODPA); 2, 6- Di- tert. butyl-4-methyl phenol (BHT); Styrenated Phenol (SP); 2, 2 methelyne – Bis (4- methyl-6-tert. butyl phenol) (BPH); are all approved by Food and Drug Administration (FDA).